ההבדל העיקרי בין FMEA ל-DFMEA הוא ש-FMEA משמש למוצרים, תהליכים ושירותים בארגונים ואילו DFMEA משמש רק לעיצובים של מוצרים.
ישנם שני סוגים של FMEA (ניתוח אפקטי מצב כישלון): DFMEA ו-PFMEA. DFMEA מייצג ניתוח אפקטים של מצב כשל בעיצוב ואילו PFMEA מייצג ניתוח אפקטים של מצב כשל בתהליך. יתר על כן, FMEA היא מתודולוגיה נפוצה שאנו יכולים לראות במגזרי הייצור וההנדסה; הם מפחיתים את הכשל הפוטנציאלי של המערכות שלהם, כמו גם את עלויות התפעול והתכנון.
מה זה FMEA?
FMEA קיצור של Failure Mode Effects Analysis. FMEA היא גישה שלבים לזיהוי כל הכשלים האפשריים בתכנון, כשלים בפעולות או בתהליכי הרכבה, או במוצר או בשירות. המתודולוגיה של FMEA מקטלגת את כל הכשלים על סמך הסבירות וחומרת הכשל. "מצב כשל" מתייחס לכל פגמים או שגיאות בעיצוב, בתהליך או בפריט, המשפיעים על הלקוח. בינתיים, ניתוח ההשפעות מתייחס לחקר ההשלכות של הכשלים.
יתר על כן, FMEA מתעד ידע ופעולות קיימים הקשורים לסיכונים של כשלים ומשתמש בהם לשיפור מתמיד. FMEA מתחיל בדרך כלל בשלבי התכנון התיאורטיים המוקדמים ביותר וממשיך לאורך כל אורך החיים של המוצר או השירות.
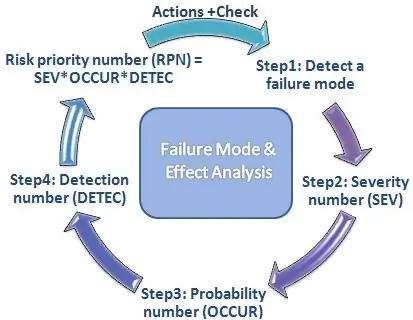
יתר על כן, FMEA היא גישה פרואקטיבית המזהה סיבות פוטנציאליות לפני כן, כך שניתן לתקן פגים גדולים בהתאם כדי למנוע פגמים גדולים. יישום זה נמצא בשימוש נרחב במגזר הייצור.
FMEA משמש במצבים הבאים:
1. לפני השקת תהליך, מוצר או שירות חדשים.
2. בעת שימוש בתהליך, מוצר או שירות קיימים בדרך חדשה
3. לפני פיתוח תוכניות בקרה לתהליך חדש או שונה
4. כשיפור מתמיד לתהליך הקיים
5. כאשר מדווחים על תלונות או כשלים חוזרים ונשנים במוצר, בתהליך או בשירות הקיימים
6. סקירה בזמן לאורך כל חיי התהליך, המוצר או השירות
מה זה DFMEA?
DFMEA ראשי תיבות של Design Failure Mode Effects Analysis. מתודולוגיה זו יכולה לזהות כשלים פוטנציאליים בעיצובי המוצר בשלב הפיתוח. למעשה, DFMEA שימש לראשונה במדעי הטילים כדי למנוע כשלים. כיום, תעשיות רבות משתמשות במתודולוגיה זו כדי לזהות סיכונים, לנקוט באמצעי נגד ולמנוע כשלים. ברוב המקרים, מהנדסים משתמשים בזה כהליך כדי לבחון את האפשרות של כשל בתכנון במצב של עולם אמיתי.
ראשית, DFMEA מזהה את כל פונקציות העיצוב, מצבי הכשל וההשפעות שלהם על הצרכן עם דירוג חומרה מתאים. לאחר מכן, הוא מזהה את הסיבות השורשיות שלהם ואת מנגנוני הכשלים האפשריים. דירוגים גבוהים עשויים לגרום לפעולות להימנעות או למזער את הסיבות ליצירת מצב הכשל. לאחר ביצוע פעולות מומלצות עבור כשלים שזוהו, השלב הבא הוא השוואת ערכי ה-RPN לפני ואחרי. RPN מייצג Risk Priority Number, שהוא הכפל של חומרה, התרחשות וזיהוי.
יתר על כן, הכלי העיקרי המשמש עבור DFMEA הוא מטריצת DFMEA. מטריצה זו מציגה מבנה לאיסוף ותיעוד מידע קשור כולל מפרטים טכניים, תאריכי הנפקה, תאריכי עדכון וחברי צוות. בדרך כלל, DFMEA היא עבודת צוות של מומחיות טכנית וכוללת בדרך כלל צוות חוצה תפקודיים. יתר על כן, DFMEA אינו מסתמך על בקרות תהליך כדי להתגבר על כשלי עיצוב אפשריים.
מהו הקשר בין FMEA ל-DFMEA?
FMEA היא המתודולוגיה הגנרית של ניתוח אפקטי מצב כישלון. DFMEA הוא סוג של ניתוח אפקטים של מצב כישלון (FMEA) שנערך עבור עיצוב מוצרים בשלב פיתוח העיצוב. שניהם מעריכים את הכשלים האפשריים, את חומרת הסיכונים, בקרות קיימות, המלצות ושיפורים לאחר פעולות מומלצות.
יתר על כן, המטרה הסופית של ניתוח אפקטים של מצב כישלון היא לצמצם או למנוע פגמים גדולים של מוצרים, תהליכים או שירותים, מה שבסופו של דבר יוזיל את עלות התכנון או התפעול.
מה ההבדל בין FMEA ל-DFMEA?
FMEA הוא המינוח הנפוץ לניתוח אפקטים של מצב כשל בעוד ש-DFMEA הוא סוג של FMEA. יתר על כן, ההבדל העיקרי בין FMEA ל- DFMEA הוא היישום שלהם. מתודולוגיית FMEA משמשת עבור מוצרים, תהליכים ושירותים בארגונים ואילו DFMEA משמש רק עבור עיצובים של מוצרים.
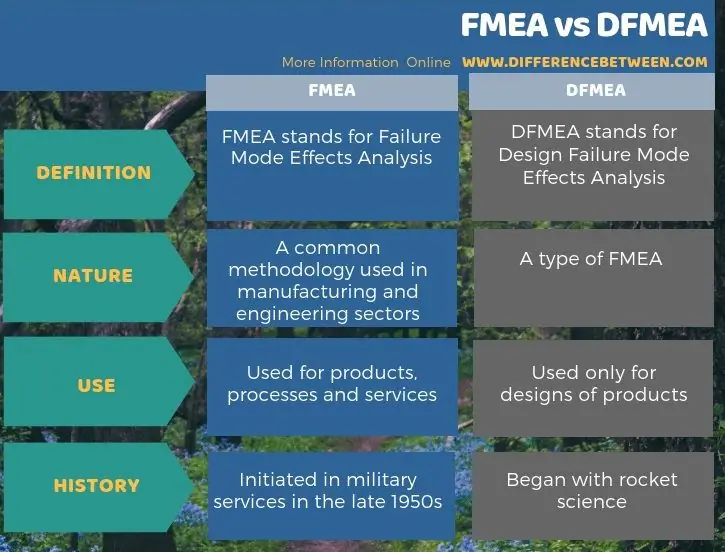
סיכום - FMEA לעומת DFMEA
ההבדל העיקרי בין FMEA ל-DFMEA הוא ש-FMEA מייצג את Failure Mode Effects Analysis והוא הבסיס למתודולוגיה בעוד ש-DFMEA מייצג את Design Failure Mode Effects Analysis וזה סוג של FMEA.